2022-06-28 Product news
Plant Pump Processes Hold Key To Greater Efficiency, Says Expert
Food and beverage (F&B) manufacturers must further refine process efficiency if they are to navigate continually rising power costs and market uncertainty, says a sector expert.
Alfa Laval’s new CPP range, DuraCirc™ allows operators to benefit from a balance between industry-leading performance, superior hygiene and simpler service.
With trade body Energy UK requesting the Government curb demand from energy-intensive commercial users due to soaring bills, Ian Forrester, Business Unit Manager for Separation and Food Systems at Alfa Laval, is imploring F&B stakeholders to analyse process components for marginal gains. However, he also underlined the need to ensure that any process changes do not harm product integrity or lead to more complex maintenance procedures.
“The food and drink industry is the largest manufacturing sector in the country, and, according to the Department for Business, Energy and Industrial Strategy, has previously been the fifth biggest consumer of energy,” explains Ian. “Any industry of this scale is going to be affected by enduring and emergent challenges, including the need to decarbonise and skyrocketing energy bills. Yet now, with the Food & Drink Federation only last month warning that 41% of its surveyed members had been impacted by rising energy prices, it is clear action must be taken.
“Processing professionals therefore need to look at their current plant components, as any minor adjustments to systems could be replicated as larger gains at scale. In this current, challenging climate, such improvements may be vital to keeping energy costs down while also enhancing performance."
According to Ian, the handling and transfer of viscous solids, fluids and fragile slurries as part of Cleaning-in-Place (CIP) – a key aspect of hygienic manufacturing plants – is one such example of where further efficiencies could be gained. Specifically, he identifies circumferential piston pump (CPP) design as an often-overlooked area for process engineers and facilities managers to address.
He continues: “CPPs enjoy widespread use in food and beverage plants, but previously, their use has often involved settling for compromised performance to guarantee hygiene standards. Yet continued innovation means this is no longer the case.
“Indeed, models that are durable, reliable, meet strict hygiene standards and achieve high volumetric efficiency alongside wide flow and pressure performance envelopes now exist. With the industry under strain, improving CIP process efficiency and using pioneering pump designs that allow for faster maintenance could make a big difference to a manufacturer’s bottom line this new year.”
Alfa Laval’s new CPP range, DuraCirc®, is one such example of these latest-generation models. Featuring a robust shaft and gear case design allowing close pump-head clearances that increase volumetric efficiency while minimising rotor contact, the pump is also designed with the low net position suction head requirement in mind. Consequently, operators can benefit from a balance between industry-leading performance, superior hygiene and simpler service.
It can achieve flow rates up to 150 m3/h (660 gpm) and handle operating pressures up to 40 bar (580 psi) – 15% higher than all other circumferential piston pumps. Importantly, the range is certified to meet EHEDG guidelines and 3-A Sanitary Standards, with a crevice-free design and product-wetted elastomers made of FDA-conforming materials, and fully interchangeable components to reduce time-consuming rebuilds and simplify maintenance.
For the most discerning applications, DuraCirc™ Aseptic is also available, using a steam barrier on all interfaces between product media and the outside atmosphere for a truly aseptic experience.
Stop settling for compromises. Find out more about Alfa Laval’s DuraCirc® here.
Tags
All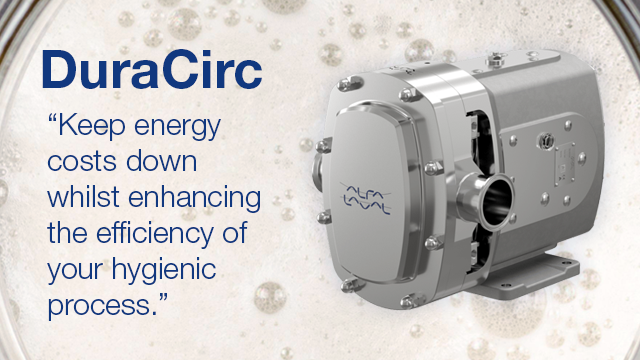