In the forefront of resource recovery
Energy efficiency is a heart cause for most any industrial plant today. Supplying technologies with great potential for resource recovery, Alfa Laval wanted to walk the talk by installing a heat pump solution for heat recovery in one of the company’s Swedish manufacturing sites. A few years later, we are more than happy to talk about the results: lower carbon emissions and drastically reduced energy costs.
DATE 2023-11-28Alfa Laval site Gunnesbo in Sweden is the home to the flagship plate heat exchanger factory, as well as the Group headquarters. Housing approximately 1300 colleagues in two office buildings and extensive manufacturing facilities, this site of over 55 000 sqm requires a lot of heat to function on a normal working day.
In a year approximately 20,000 gasketed plate heat exchangers and 4,500,000 heat exchanger plates are produced; a great load on the plate pressing line and the system for cooling the lube oil used in the process. This generates a lot of heat, and before 2013 this was just vented externally.
Since 2013 however, Alfa Laval is recycling this waste heat into the system that supplies the total site including the tap water system for a greater part of the year.
“This installation has really proven to be a success for us,” says site manager Arne Hermansson. “Not only do we get to enjoy fantastic energy cost-savings, but this installation has also become a convincing show case for how Alfa Laval can support our customers to turn waste energy into a useful recyclable resource. The green aspect is very important as most customers are striving hard to find new ways to minimize their negative environmental impact”, he concludes.
Another green fact adding to the story is that the cooling is based on a future-proof natural refrigerant. “We chose to work with ammonia since this is the most efficient of the natural refrigerants”, says Jesper Olsen, Application Expert Refrigeration, and who is the core of the brain thrust behind the solution. “We promised to double the coefficient of performance based on our previous experiences…and we did!”, he says. And while achieving this high efficiency, the system is only requiring a very low ammonia charge which for specific customers is extremely vital. Olsen concludes:
“A solution like this is dependent on local conditions like weather and possibility to use the recovered energy. In this part of the world, Sweden, it is easy to do so. However, we have seen that a lot of companies in various industries can reach the same energy efficiency, lower costs and reduced environmental impact as we have done. It feels good that we as a manufacturer can practice what we preach.”
The technical solution
The heat pump solution for energy recovery uses a general high-pressure cycle with three plate heat exchangers at the core of the solution:
- The evaporator, an Alfa Laval MK15-BWFGR semi-welded unit with a U-Turn separator, combines four separation methods: agglomeration, gravity separation, centrifugal forces and surface tension.
- The Alfa Laval M10-BWFT semi-welded unit is the condenser producing 65°C heating water.
- District heating is handled by an Alfa Laval TL10-BFG.
- There is also a substation for heating and tap water in the room that utilizes brazed heat exchangers from Alfa Laval.
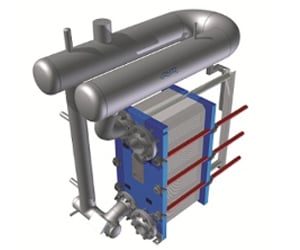
The result in figures
- Energy consumption has gone from 3,700 megawatt to 1,850 megawatt per year
- Carbon emissions have been reduced with emissions by 140 metric tons, which equals 40 return flights from Sweden to the Canary Islands.
- The hold-up volume of ammonia: 40 kg
- Payback time: 3 years
- Estimated energy cost savings: 55%
- Service intervals:
10 – 12 years for the condenser
15 – 17 years for the evaporator
Tags
All