Welded spiral heat exchangers
Alfa Laval spiral heat exchangers are designed to handle the toughest heat transfer challenges. Whether it’s frequent fouling from dirty media, or limitations from pressure drop and floor space, they are the ultimate problem solver for liquid-to-liquid and two-phase duties. The robust, efficient and compact designs keep both installation and maintenance costs extremely low, and they have a proven reputation for almost never fouling up.
Improving sustainability with Alfa Laval’s spiral heat exchangers
- Minimal fouling, or clogging, in duties involving very dirty, highly viscous or particulate media, ensures uptime
- Easy-to-open design makes cleaning quick and simple, ensuring low maintenance costs
- Reduced pipework and steel structures means lower installation costs
- Increased energy savings and reduced emissions thanks to thermal efficiencies 2-3 times higher than comparable shell-and tube exchangers
- Each unit is fully customized, offering the best thermal fit for the specific duty
Downloads
Case stories
Product leaflets
Improving sustainability with welded solutions from Alfa Laval
Alfa Laval welded heat exchangers maximize energy efficiency and heat recovery, with innovations that deliver exceptional thermal performance and reliability, for a wide range of duties. But it’s more than technology. It’s also the people: experienced experts with deep process knowledge and a global service presence. Combined, that’s how you improve sustainability.
Working principle
Alfa Laval spiral heat exchangers are circular units containing two concentric spiral flow channels, one for each fluid. The different media flow counter currently: one fluid enters the centre of the unit and flows towards the periphery, the other enters the unit at the periphery and moves towards the centre. The channels are curved and have a uniform cross section. There is no risk of intermixing.
The product channel is normally open on one side and closed on the other. The channel for the heating/cooling medium can sometimes be closed on both sides, depending on the cleanliness of the heating/cooling medium. Each channel has one connection in the centre and one on the periphery of the heat exchanger.
Design
The spiral geometry, with a single channel for each medium and continuous curving, is highly suitable for fluids that tend to cause fouling. This design results in high flow turbulence with resulting high shear stress, dramatically reducing the risk of fouling.
The single-channel geometry also creates a scrubbing effect that we refer to as the SelfClean™ design. If fouling does occur in the heat transfer channel, the cross-section of this part of the channel is decreased. However, since the entire flow must still pass through the channel, the velocity increases, the resulting fluid force then flushing away any accumulations of deposits as they form.
Compare this design with shell-and-tube heat exchangers where the flow enters different tubes in parallel. When tubes start to foul, pressure drop increases pushing the fluid to find alternative flow paths. The result is that fouling and clogging of the tubes happens very quickly. With Alfa Laval spirals, on the other hand, fouling and clogging is virtually eliminated.
SpiralPro
SpiralCond
Frequent cleaning a thing of the past
Mexichem, a global leader in plastic piping systems and in the chemical/petrochemical industries, needed to increase its production capacity to meet market demands.
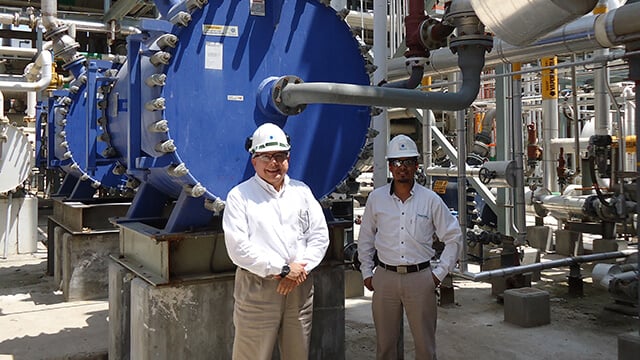
The ultimate solution to fouling problems
Leuna Germany’s MIDER refinery, owned by Total S.A., originally installed two tubular heat exchangers for cooling bottoms product in their fluid catalytic cracking unit.
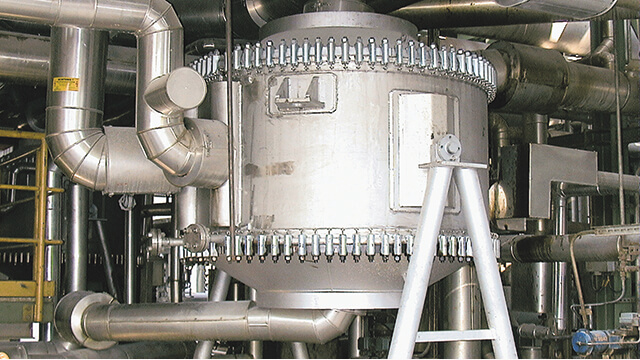
One of the world´s largest zinc producers
"We use these units because they’re very strong and very easy to clean and of course because the thermal efficiency is high." - Francisco Tarmago, Technology Manager, Asturiana de Zinc
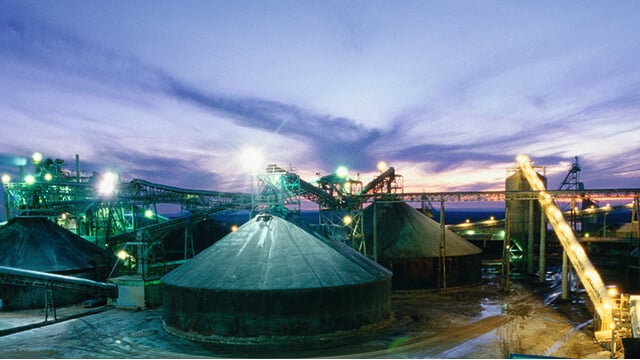
Unique features
Compared to other heat exchangers used in similar applications, Alfa Laval spiral designs offer a more compact footprint with increased thermal efficiency.
They are also built with unique features that ensure the most reliable performance:
Contact us
We will be happy to discuss the benefits a welded spiral heat exchanger can bring you and show how we can help improve your operation.
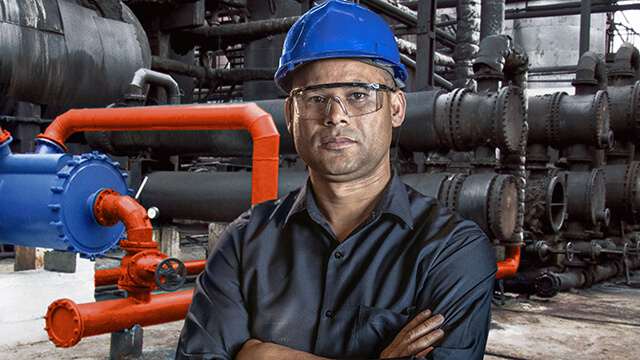
Alfa Laval energy news on LinkedIn
Our showcase page with the solutions you need to stay ahead.
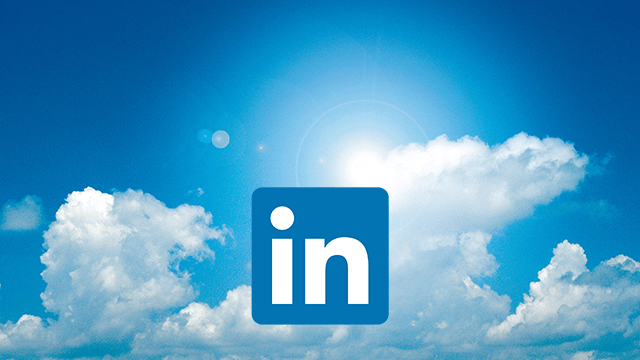