The circular future
Today, we live in a linear society that relies on fossil resources to function. But if we want to create a better future for the next generation, we need to make it circular. Here at Alfa Laval, we have the technology to support a circular landscape and the use of renewable feedstocks for all production processes instead of fossil fuels.
To be able to reach the Paris agreement net zero targets, the world’s industries must become carbon neutral by 2050. That means that we need to stop using raw fossil materials as soon as possible. This is no easy feat, as carbon is the foundation block in practically everything around us. It is in everything, from the clothes we wear and the plastic we use, to the fuels in our cars, airplanes, and ships. So, in the liquid fuels and chemical industries, where decarbonization is not an option, we can turn to defossilization instead. This means that we can still do our part for the planet, shifting away from fossil-based carbon to renewable carbon.
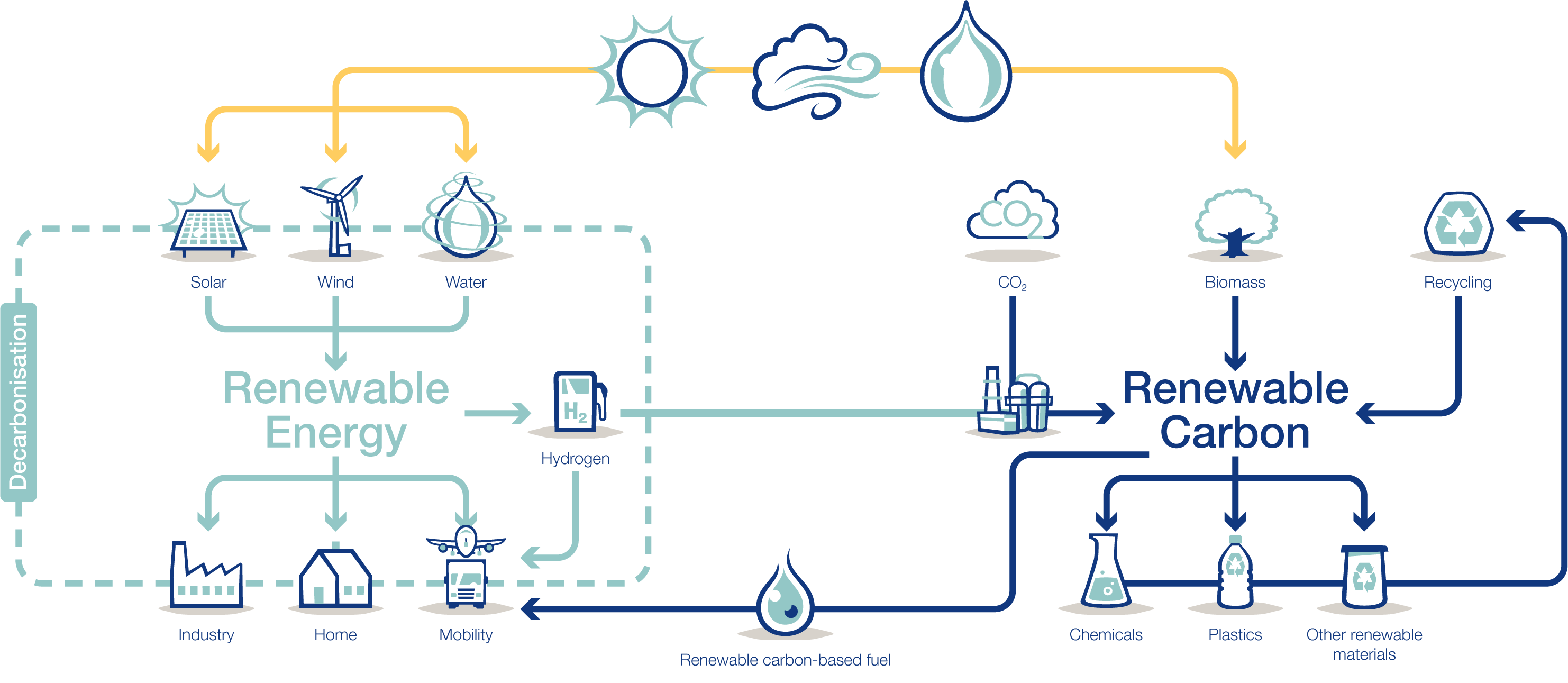
What would a circular landscape look like?
We all want to reach our net-zero targets, but what would a circular future look like? Here at Alfa Laval, we have tried to illustrate what we see happening around us and what areas our customers are currently active in. This has resulted in “The future circular landscape” - our vision of what the future circular economy could look like.
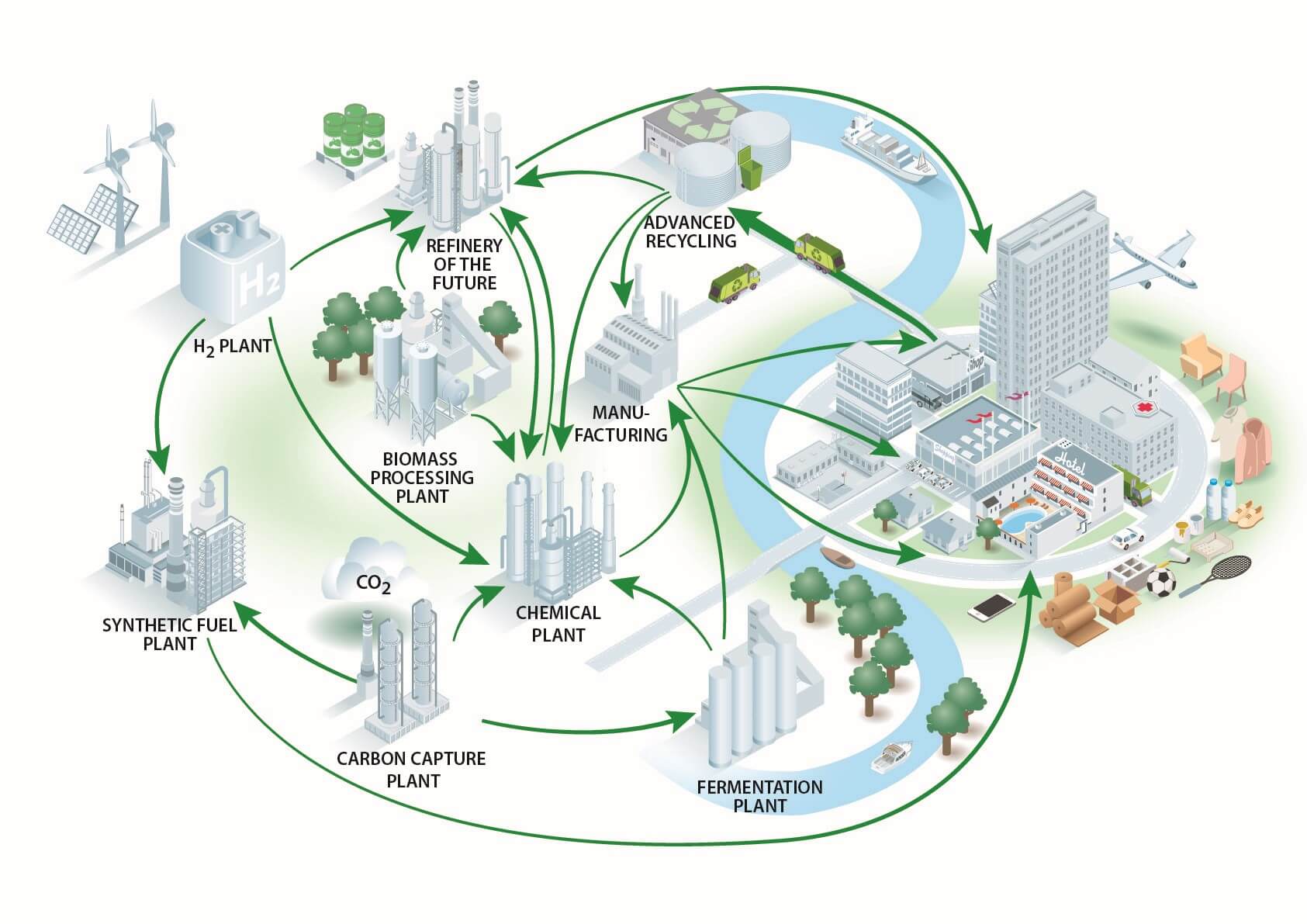
The three renewable carbon feedstock
A future circular landscape is based on the three renewable carbon feedstock that are available today: Captured carbon, biocarbon and recycled carbon. We need to implement these three types of renewable carbon in plastic, cloth, and liquid fuel production so that we can transition away from fossil fuels and reach net zero CO2 emissions by 2050.
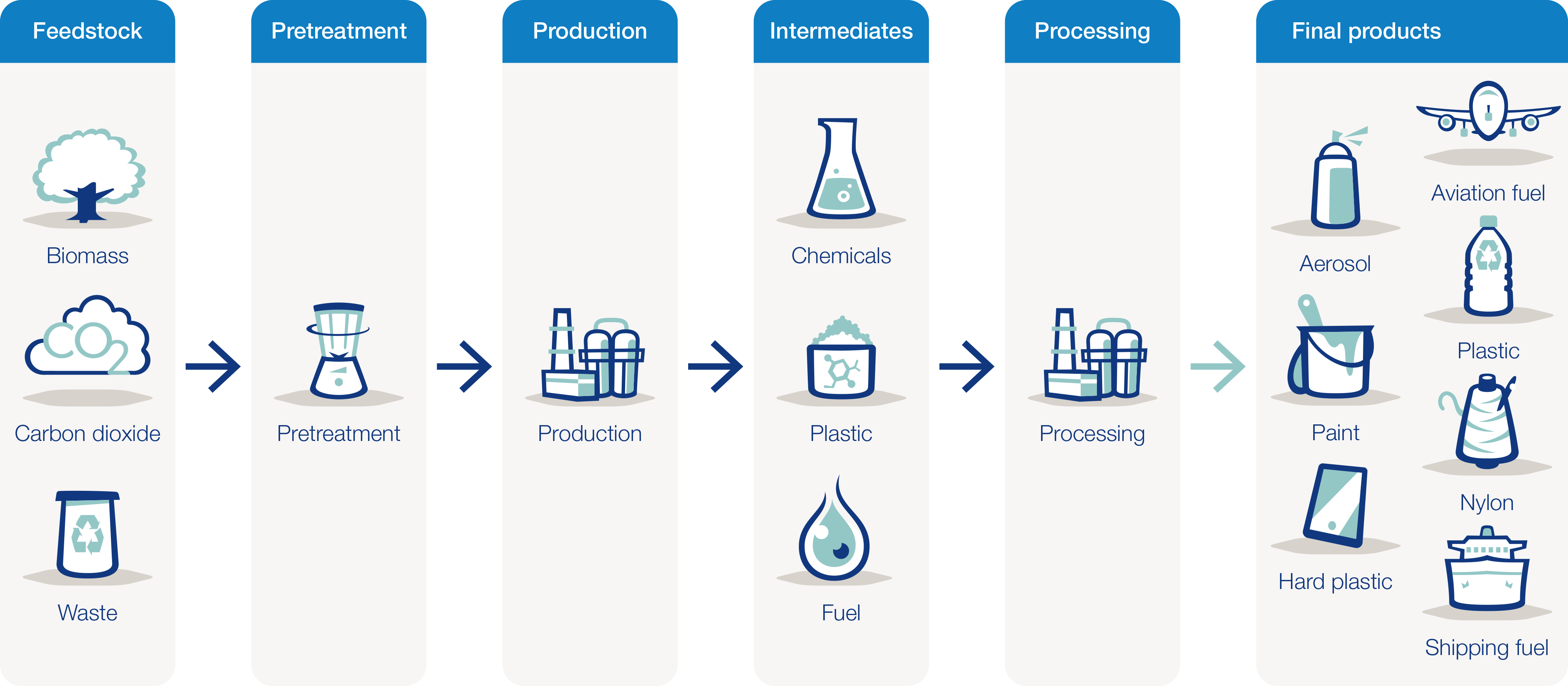
The three renewable carbon feedstock
Captured carbon
Carbon capture and utilization is a new technology that will be important in the future. In fact, it is estimated to stand for about 25% of the renewable carbon we can use. Carbon can be captured directly from the atmosphere, or from CO2-rich off gas. This carbon can be used in fermentation plants through gas fermentation, or it can be thermochemically converted into fuels and chemicals.
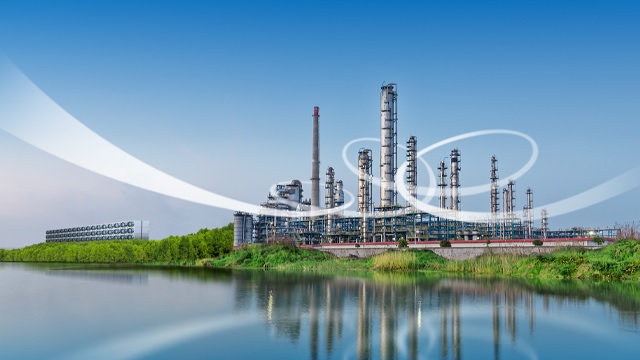
Biocarbon
Carbon in sugar, cellulose, and vegetable oil, for example, is the most used form of renewable carbon today. It will also be an important carbon source in the future, as it is estimated to stand for around 20% of the renewable carbon we need. Biocarbon is very diverse and can be used in fermentation processes, in biomass processing plants (thanks to gasification or pyrolysis), and as an HVO feedstock in the refineries of the future.
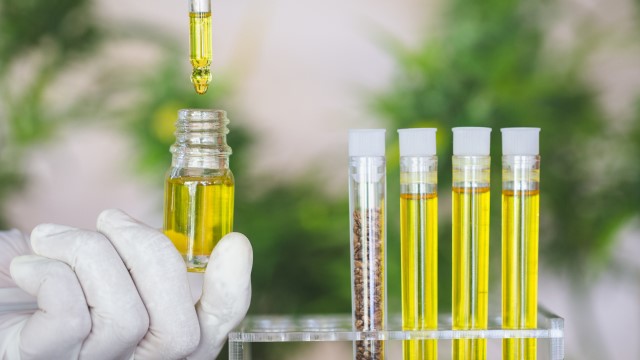
Recycled carbon
Recycled carbon is what we get back from recycling plastic, chemicals, and building materials etc. This will be extremely important in the future, as it is projected to stand for as much as 55% of the carbon we need in the future circular landscape. It can be provided through smart and advanced recycling plants that depolymerize and then polymerize plastic. Or, where this isn’t possible, it can be provided though pyrolysis to obtain circular polymers and chemicals.

Applications overview
Bioplastics
Bioplastics, or bio-based plastics, are plastic materials produced by industrial fermentation from renewable biomass sources instead of fossil fuels. In the race to reach our collective sustainability goals, bioplastics are being used as a more circular solution to conventional petroleum plastics.
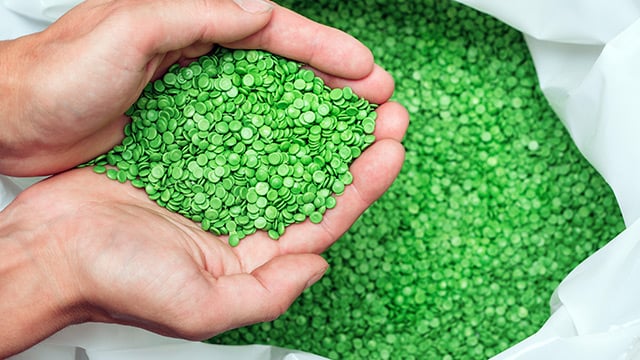
Pyrolysis
Pyrolysis is a thermal process in which materials decompose at an elevated temperature in an inert, oxygen-free atmosphere. Virtually any source of biomass or waste can be used for pyrolysis, making this an increasingly interesting solution for the renewable and recycling market. It can be used to make oil from, for example, wood and sawmill waste, used waste tyres or mixed plastics recycling.
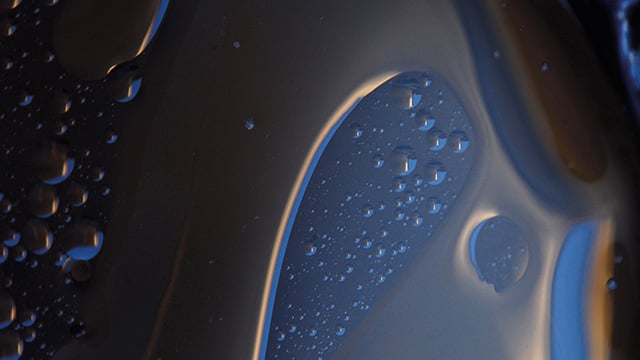
Downstream separation in renewable polymers
Renewable feedstocks like recycled material, biomass, captured carbon, and organic waste oil will be essential in defossilizing the plastic industry. But to guarantee their success, downstream separation is a key step in the process. With the support Alfa Laval technology, plastic producers can minimize product losses, obtain high product quality, and reduce water and energy usage.
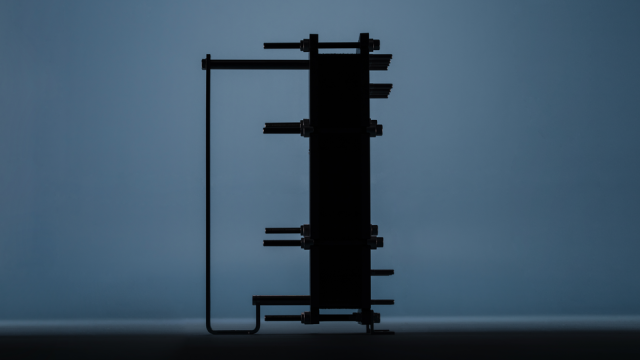
Concept Zero
At Alfa Laval, we are committed to decarbonization and aim to become carbon neutral by 2030. We will do this by eliminating the emissions from our products all the way from the raw materials we use to end-of-life. Concept Zero is a crucial step on this journey, pushing the boundaries to develop a truly carbon-neutral plate heat exchanger with no misleading schemes.
Contact us
There’s no denying that the switch from fossil-based carbon will take a massive amount of work, but it is no longer a matter of how, it is a matter of when. At Alfa Laval, we’re ready to make it happen today. Contact us to learn more!