Save resources by efficient cleaning of your industrial fluids
Water-based service fluids such as coolants, cutting fluids and wash liquids are essential to a wide range of metalworking, machining, and manufacturing processes. However, if they’re not treated in the right way, they can cost your business more than they need to. Using high-performance fluids to either wash components, or to cool or lubricate in production steps, secures efficiency and consistency in operations. Cleaning the coolants, cutting fluids or wash liquids on a regular basis significantly prolongs the service life of your fluids and, by extension, the service life of your system.
The centrifugal separator is a proven, sustainable technology to treat contaminated industrial fluids by removing tramp oil, fine metal cuttings, dirt, and sludge. The three-phase separation efficiently handles all fine particles down to one micron and removes virtually all the contaminating oil but none of the additives, in a one continuous operation. This contributes to a healthier working environment by reducing bacterial growth which is also harmful to the fluid. Other results are reduced tool wear, fewer rejects, and an overall improvement in quality. Explore Alfa Laval’s range of separators for the cleaning of industrial fluids and learn more on how you can maximize productivity, efficiency and limit environmental impact.
Benefits
-
Prolong tool and fluid lifetime
-
Increases uptime and productivity
-
Cleaner components, improved end-product quality
-
Healthier work environment
-
Reduced waste and replacement/disposal costs
Product portfolio
Alfa Laval has a range of proven disc stack separators to extend the service life of all kinds of industrial fluids and, by extension, your systems, whether you’re a small workshop or a large plant. Depending on your needs for cleaning of water-based metalworking fluids such as synthetic, semi-synthetic and soluble oils, Alfa Laval offers fixed and mobile solutions for smaller individual tanks with the Alfie 200 and Alfie 500. For larger and centralized systems, the AlfaPure series is the recommended solution.
Separator service kits and spare parts
An Alfa Laval centrifugal separator will perform for decades if you look after it properly. We offer high-quality separator service kits and durable parts, designed to simplify maintenance, boost productivity and maximize uptime. Our service kits include what is required for every specific service as described in your manual, with genuine spare parts and a comprehensive package of detailed service instructions. Explore our service offering for our industrial fluids cleaning separators and visit our webshop to order your kit today!
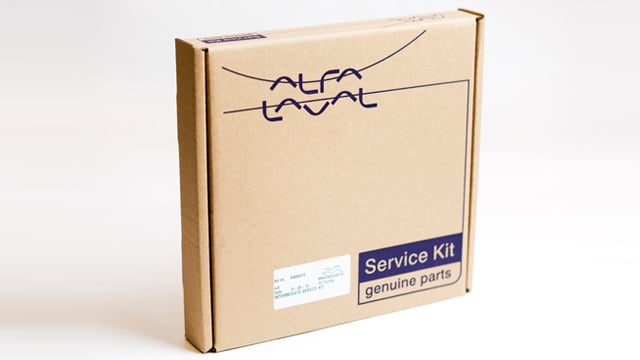
Superior cutting efficiency using centrifugal separation
Cutting fluids are an integral part of many metalworking and machining processes, functioning as a coolant and lubricant in various aspects of the production set-up. In any machining operations it’s essential to use high-performance fluids if you wish to maintain efficiency and consistency. The challenge is that the industrial fluid can easily become contaminated if they’re not properly cleaned or maintained.
As these fluids are involved in heavy cutting and drilling processes, oil can find its way into the mixture. Once the oil level exceeds 2%, the system needs to be stopped whilst the fluid is changed. Disposal and replacement of various cutting fluids can be costly and have a direct environmental impact and on operations. In addition, micro particles can also contaminate the industrial fluid, which can result in a sand-blasting effect on the components surface.
The solution is centrifugal separation. Alfa Laval equipment can efficiently separate the industrial fluid from contaminants, ensuring less downtime, reduced tool wear, extended service life of coolants and lubricants, as well as reducing the risk of damage to the cutting and drilling areas.
Increase the lifetime of your wash liquids
Wash liquids are essential to a wide range of service processes, but because they’re used to remove oil and dirt from finished components, the wash liquid itself becomes contaminated over time. When it comes to cleaning wash fluids, the replacement process can be costly due to disposal and downtime. Normal filtration gets rid of most, but not all, which means that roughly every four weeks the system needs a full clean, and the wash liquid needs to be totally replaced.
There’s also the costly process of disposing of the tramp oil, which must be taken away to an authorized disposal location. All of this can add up to significant downtime. Thankfully, with the right methods, you won’t need to do this nearly as often and they can be implemented into your process eliminating the need to shut down your process as often.
By using an Alfa Laval disc stack separator, you can ensure that the wash liquid stays cleaner for longer. Rather than closing the process every four weeks, you can extend the period between disposal and replacing the wash liquids to at least twice the period. This gives you an almost immediate return on investment.
Why use centrifugal separation for cleaning industrial fluids?
Working principle
During the separation process, the centrifugal force presses the heavy particles present in the service fluid outwards against the walls of the separator. These are discharged automatically from the bowl to the sludge tank. If two liquid phases are present (such as coolant and tramp oil, or neat oil and water), the centrifugal force will cause the two phases to separate. The light phase and heavy phase exit separately through different outlets of the separator.
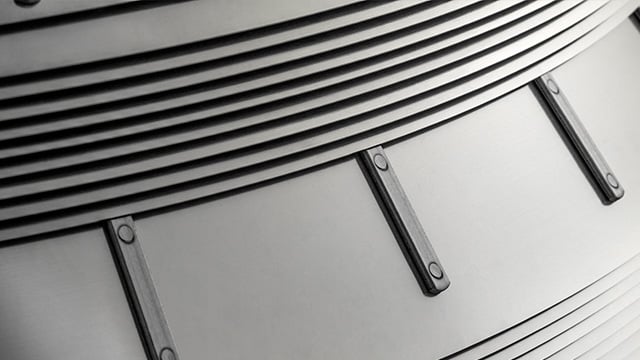
The four technologies in brief
- Centrifugation separates matter of different densities – both oil and particles
- Filters use different mesh sizes to capture solids only
- Skimmers use an oleophilic collecting device like a belt or a disc to collect oil
- Coalescers remove oil from industrial fluids
The best technology is the one that suits your application
- Centrifuges direct clean industrial fluid back into your process while the separated contaminant is continuously discharged. Particles are contained in the separator bowl for later disposal or are discharged automatically.
- Filters commonly capture solids in a disposable cartridge, which needs replacing regularly.
- In skimming, the oil adheres to the outside of a floating, closed-loop tube as it is drawn across the surface of the water, adjusting automatically to changing water levels.
- Coalescers can only work if the industrial fluid is almost particle free. Most often, a coalescer is used in conjunction with filters to ensure the removal of solid particles and water in one system.
Cleaning technologies compared
11 benefits with centrifugal separators
1.
You get an extremely effective separation of both liquid and solid contaminants. This means that you can safely use your cutting liquid 2–6 times longer than with simpler cleaning mechanism.
2.
Cleaner cutting fluid also increases precision and extends the life of your equipment. This means that you boost productivity and save money since you don’t have to replace tools, filters, valves, and pumps as often.
3.
When you use the same cutting fluid longer, your costs for buying new and disposing of old cutting fluid decrease considerably
4.
Changing cutting fluids less frequently also diminishes your environmental impact: the creation of new cutting fluid, the destruction of the old one, and transportation all affect the environment negatively.
5.
Alfa Laval centrifugal separators can manage difficult conditions such as large cleaning volumes and a temporary high influx of oil
6.
When used, cutting fluid creates a mist that can be inhaled or come in contact with the skin of your employees. This is hazardous if the cutting fluid contains fungi or bacteria. Cleaning your cutting fluid effectively, therefore, improves the working conditions of your staff greatly.
7.
To avoid the growth of bacteria and fungi, some suppliers add toxins to their cutting fluids. This is not good for the environment – bacteria and fungi are best avoided by efficient cleaning
8.
The operational cost of Alfa Laval centrifugal separators is very low, as is the service cost. You need to make an initial investment, but the total cost of ownership (TCO) is low.
9.
Alfa Laval is there for you. The company’s service organization is recognized as the best in the world within this area
10.
Alfa Laval is a pioneer within separation and has supplied high-quality centrifuges for a large number of applications for more than a century
11.
An Alfa Laval centrifugal separator has superior quality and will perform for decades if you take care of it correctly. In short, it’s a matter of reading the manual and using genuine parts and the right tools. There are specific service kits with genuine spare parts and a comprehensive package of detailed service instructions
Save resources by cleaning cutting fluids
Cutting fluids are an essential part of many machining processes, and without the right care and attention they become contaminated and can cause problems. By effectively cleaning your cutting fluids, you can avoid these issues and reduce your overall operating costs. In this whitepaper we explain the pros and cons of the different cleaning methods, and help determine which is best for your business.
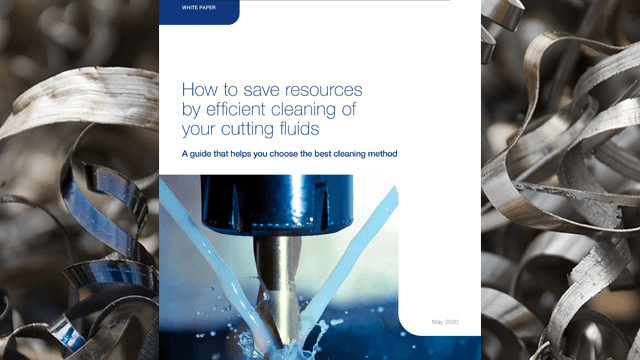
Customer stories
Customer case: Alfa Laval
Alfa Laval’s production unit in Eskilstuna improves the efficiency of 40 metal working machines by cleaning the cutting fluids. The fluids are efficiently cleaned by a separator in an integrated in-loop system.
Customer case: Outokumpu
Outokumpu, the global leader in stainless steel, was able to maximize production efficiency while reducing its carbon footprint by using a range Alfa Laval equipment. The new way of working also results in less scrap, and better quality in the final products.
Visit webshop
The Alfa Laval webshop help you to filter, select and quote the best solution for effective cleaning of coolants, wash liquids and lube oil. Enter the online catalogue and find your selected products and parts now. If the products are not visible for your country, please fill out the contact form.
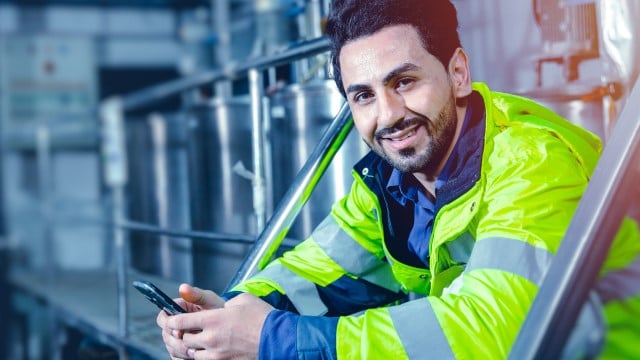
Let's talk!
Get ready to improve productivity and reduce equipment lifetime costs. Have any questions about cleaning of wash fluids and coolants? Need help choosing the right solution? Contact us to learn more about how our industrial fluids cleaning solutions can help your business. Simply complete the form and we'll get back to you as soon as possible.