Service Agreements
Alfa Laval Service Agreements are tailor-made service solutions that combine any of our services, based on your specific needs. To maximize your performance and reduce your operating costs, these agreements bring you peace of mind by minimizing the risk of unexpected breakdowns. They also give you full control over your maintenance budget.
Alfa Laval Service Agreements give you:
☑ Maximum uptime
☑ Short payback time
☑ Full control over maintenance budget
Looking for a specific service?
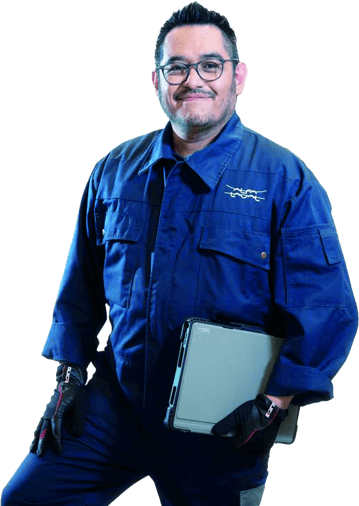
Building Trust by Increasing Operating Efficiency & Minimizing Costs
Maximum uptime & efficiency:
Regular maintenance keeps your equipment running at its best and working when it should work. It also makes sure that performance is at the highest and intended level.
Guarantees / Warranties:
Keep your warranty valid and prolonged in time. Often warranties are not valid unless the machine has been served properly.
Short payback time & equipment lifetime:
A well-maintained machine runs for a very long time. Many decades or half a century is not unusual. This is smart economy and the right choice for this type of capital investments.
Full Control Over Maintenance Budget:
A maintenance plan means you will know upfront well in time when the service is going to be performed, and what services we will deliver. Spare parts will be ordered and delivered by us. And you will also know upfront how much it will cost you.
Risk Reduction:
Not serving the equipment is united with several risks, lower or failing performance – bad output, breakdown situations with costly repairs or destructions of the equipment etc. It can potentially also create a dangerous workplace for any humans in the close vicinity of the equipment.
Service Patrol - Regular Audits
Every accident starts with a small fault.
Service patrol service signed in the service agreement will let Alfa Laval send experienced service engineers to visit your separators and process on-site, listen to you, check equipment status (without disassembling and assembling), discover small problems at an early stage, and fix them A.S.A.P.
According to information collected on-site, specialists will give relative recommendations to optimize the performance of separators and processes.
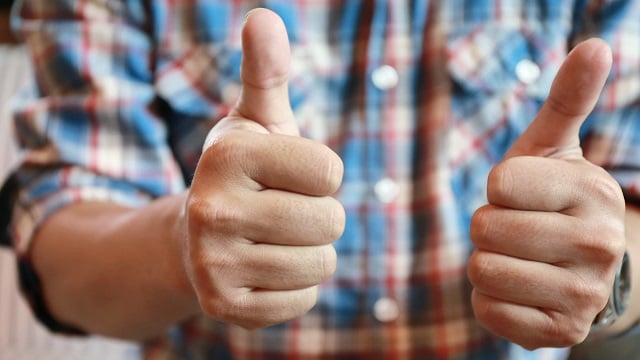
Planned Prevention for Processing Success!
Every service patrol will create a formal service report and be kept on both sides. Service patrol service included in a service agreement can help you achieve a regular audit of the equipment in their production site. During Performance Audits, an Alfa Laval process specialist evaluates the status and performance of your equipment is evaluated and makes recommendations on service measures and process adjustments.
Potential problems are discovered at an early stage and a comprehensive report is produced. Allowing us to plan for all your service events including procurement of all spare parts gives you a predictable service budget with no nasty surprises!
What is an Alfa Laval Service Agreement?
Service agreement customers are prioritized and protected. An exclusive offer to our service agreement customers is the prioritization of your service needs. Based on our experience with other customers we know this has huge value when a problem arises.
Compared to service execution without an agreement, Alfa Laval plans all service events including procurement of all spare parts. Planning future service requirements allows you to have a predictable service budget. Customized solutions with services exclusive to service agreement customers (e.g. service patrol) are built on 3 building blocks:
Scope of equipment - forms the foundation of the agreement
Can be single individual equipment, many pieces of individual equipment, or modules built on many pieces of equipment and components. It can also be complete systems, containing modules and equipment. The scope of equipment is selected by you as a customer with our support and recommendations.
Scope of services – “The service products” or “Services”
Service products are for example, spare parts (for instance kits), maintenance work (hours), audits of processes and/or equipment, training, various types of digital services, and many more. The Alfa Laval service portfolio is vast and contains ALL services that can optimally maintain your Alfa Laval equipment.
The scope of services is selected by you as the customer. We support with recommendations based on the equipment in question, your production situation, end products, and demands on processes. These services are what you chose and commit to buy from us and what we commit to deliver to you as a customer.
Service schedule – Timing of service
The service schedule is the services planned in time and in a “calendar” which indicates what services will take place at what time. Based on the equipment and the running hours and the specific (end-)product being produced, we make maintenance recommendations for you.
The complete service agreement is always a customized solution based on your specific needs and situation. In addition, an agreement also includes commitments from both sides. Our commitment from Alfa Laval is to deliver according to the agreement and your commitment as a customer is to hire us for agreed services in the contract and we jointly follow the service schedule.
Services
An Alfa Laval Service Agreement can include any service in our 360° Service Portfolio. We recommend:
- Preventive maintenance – 100% equipment availability and performance.
- Service patrol – an Alfa Laval specialist evaluates the status of your equipment and makes recommendations.
- Genuine spare parts – for operational reliability of your equipment and no need to revalidate your process.
- Technical and GMP documentation – all the necessary documentation after each service.
- On-site assistance during operation – An Alfa Laval service technician checks your equipment before process and during operation.
- Training – training courses for your staff, covering everything you need to know to safely operate and maintain your equipment.
- Condition monitoring – allows you to optimize maintenance and increase uptime by monitoring condition with immediate alerts if actions are required.
- Remote support – With remote support you have direct access to our service technicians via online video.
Learn more about our complete portfolio of services
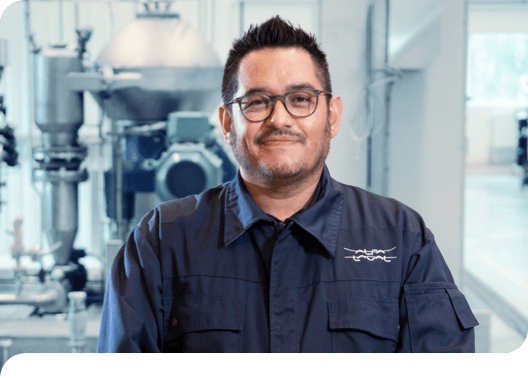
On-site Operating Assistance
On-site operating assistance means that Alfa Laval can arrange service specialist to your site, helping your process critical batch of production. This will help maximize the reliability both for heat exchangers, centrifuges separators, decanter centrifuges and process, protecting your high value products.
For some, having peace of mind is of utmost importance. By having an Alfa Laval service specialist on-site to perform the job, you do not have to worry about operating the equipment at this step, therefore, can focus on other critical parts of the whole process. It helps relieve the stress of having to operate your equipment from your mind.
🗸 Equipment check-up before operation
🗸 Allows your personnel to focus on other critical parts of the process
🗸 Avoid hiring a dedicated operator, and save on labour cost
For those who lack labor resources or experienced operators, the service is a big lifesaver, so they do not have to hire an additional resource.
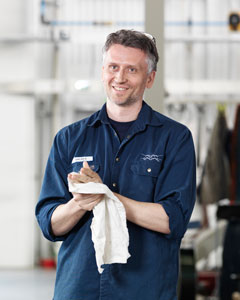
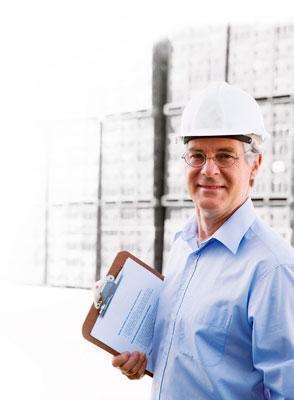
Risk-based Approach: Ensure Safety & Integrity are Maintained On-site
Incorrectly performed maintenance can have devastating results.
Non-genuine parts do not have the same specifications and entail risks to your production. Non-genuine spare parts can't keep the identical measurements and materials with the genuine ones. They could bring risks like leakage, high vibration, contamination and even breakdown.
Genuine spare parts with certificates are in accordance with GMP. By using genuine spare parts, you avoid having to revalidate your process because of spare parts change.
Our service secures your machine as it was when it was validated. Genuine Alfa Laval spare parts, lubricants, etc. are always used to ensure the same quality of materials and components.
There is no risk of contaminants from materials, substances for operation from the maintenance engineer, or any other potential source that can cause risk for your workers and customers.
Service agreements for biopharma producers
Discover a tailor-made service solution based on your specific needs in biopharma industry. Maximize equipment availability, process yield, product quality and patient safety in biopharma applications with an Alfa Laval Service Agreement.
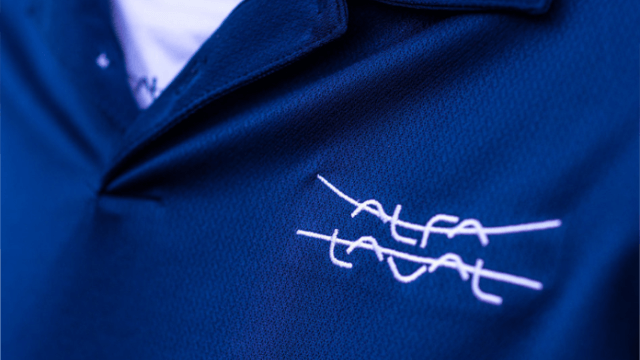
How it works
Our experts:
- Discuss with you expected results, based on your goals and needs
- Define tailored scope of services
- Carry-out services on schedule, as planned, with continuous follow-up
- Hold yearly review and improvement meetings to identify new opportunities and secure continuous improvement
Contact us to know more about Alfa Laval Service Agreements